 |
 |
Wonderpack shall be unveiling an addition to their existing N Series
Roll fed High Speed Trim-in-place Thermoforming machine a new Model IM 4065 N2K machine.
It occupies less floor space as compared to theearlier machines and has more forming area
of 650mm x 400mm. This machine can produce upto
900 tones of finished products per annum.
Machine with thermoforming counting, label placing, bag making, and Shrink Wrapping can
be just handled by one person. If integrated through Wonderpack Uniforma Series, it will
have the lowest cost of processing.
|
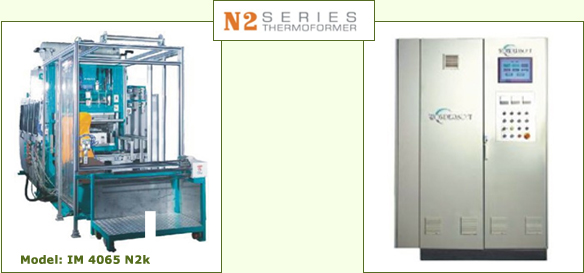 |
Wonderpack would be displaying 8 cavity vegetable tray in polypropylene
mould having dimensions 180mm x 132mm for demonstration. Earlier model IM 3560 N2K used to
accommodate only 3 cavity mould of similar vegetable tray. Therefore, there would be an increase
in productivity by 2.75 times.
REMOTE SCRAP WINDER:
It has remote scrap winder assembly for easy handling of scrap and easy tool change.
CONTROL PANEL:
It is designed and manufactured with latest CE standards compliance which tested machine for the following:
 |
Power frequency test |
 |
RF Radiated (RS) test |
 |
ESD (Electro Static Discharge) test |
 |
Fast Transient test |
 |
Surges test |
|
 |
Voltage dips test |
 |
Voltage interruption test |
 |
Emission test at enclosure port |
 |
Emission test at AC mains port |
 |
Acoustic Noise test |
|
|
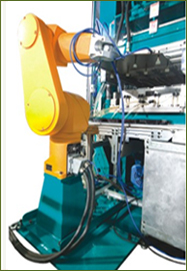 |

Its Robotic arm provides perfect stacking-solution for products like trays/punnets which is
otherwise difficult with the conventional stacker.
This enables stacking without any increase in manpower, on changing of the programme it enables
the Robotic-arm to pick and place other products as well.
Robotic stacker Model RS 25 can also be programmed to count the stacks.
The individual thermoformed items are stacked with the help of robotic stacker. The robotic
stacker consists of robotic arm and the kit gripper using up to 6 axis servos and it is placed
in front of the thermoforming machine.
After the product is thermoformed, the items are picked by the robotic stacker and placed on the
conveyor belt or magazine as per the product shapes. The number of product on a stack can be
programmed as per requirement and as soon as the preset count is reached the conveyor belt moves
forward to deliver the stack to the following packaging unit like BG 200 or further processing unit
like Hole Punching Press, rim rolling, Bag making, etc. |
|

Perfect on-line packing of products can be done.
This packing line requires less manpower as such indirect saving on operational cost is done.
Its packing speed can be aligned with Out-put speed of Thermoformer.
REMOTE SCRAP WINDER:
 |
Single machine can process up to 900 Tons of finished good |
 |
Machine could be backward integrated with a sheet extruder with synchronized controls for both sheet extruder
and thermoformer and forward integrated with inline grinder with close loop recycling system through Automatic
Ratio/Hopper Loader. |
 |
Machine gives lowest per kilo processing cost |
 |
Feature like servo plug assist can optimize sheet thickness to save material up to 15% |
 |
All above means improved profitability in today’s competitive market |
Machine strongly recommended for following market segment:
 |
Horticulture applications like vegetable trays, Food trays, punnets |
 |
Flower pots, seed pot, seed tray, and berry box etc. |
 |
Household semi-disposable like storage & Serving containers with lid |
 |
Processed Food Packs |
 |
Dairy container |
 |
Lid for containers |
|
COME & EXPERIENCE A NEW WORLD OF THERMOFORMING
WITH WONDERPACK AT K2007... Hall No.3, Stand No 3G35 or
www.wonderpackindustries.com or www.machinesforplastic.com
|
 |
Click Here To Contact Us |