
ARTICLES
Global demand for Polyethylene is estimated to grow from 79 MMT in 2012 to 99 MMT by 2017, driven largely by increased demand in high population growth Asian countries and the rapid economic development of numerous transition countries in the Asia Pacific region, Central Europe, Middle East and South America. North American PE producers are establishing a cost advantage in a highly competitive global market expected to continue from 2012 to 2017. Read more in Cheaper natural gas feedstock from shale to revitalize North American Polyethylene business
Bioplastics are estimated to grow to 7% of the total plastics consumption by 2020. Some of the growth drivers will include recyclability and degradability of bio-based materials, reduction in application development and technology licensing costs, growing customer awareness. The sector will also benefit from mandates in Europe and Japan favoring compostable/recyclable materials, large investments by leading petrochem makers. Improved properties will increase the share of biorenewable materials in various packaging applications. Asia Pacific’s demand is expected to grow rapidly, boosting demand for bioplastics, particularly in flexible packaging applications. Read more in Large replacement demand from packaging to boost demand for biorenewable materials in Asia-Pacific
In packaging applications, food that is being wrapped or stored in a plastic container usually has high moisture content. When this packaged item is stored in a cool environment, the moisture condenses on the surface causing fogging to occur. Depending upon the application, this fog is typically not considered aesthetically pleasing and may impact food spoilage.
There are two routes the packaging industry uses to minimize the formation of fog on sheet, film or thermoformed articles. Read more in External and internal antifog agent options for biopolymers
American polyethylene producers are big beneficiaries of the shale gas boom. Ethane is primarily produced when passing natural gas through crackers. On converting the low cost ethane into ethylene, U.S. PE producers now have a major feedstock advantage. However, more complex hydrocarbons derived from crude oil are becoming more expensive and their supply more volatile, adding urgency to a drive by specialty chemical companies to turn to bioplastics. While concern about oil scarcity and consumer demand for renewable products have been long-term drivers of bioplastics research, production of shale gas by hydraulic fracturing has added to the investment case. Read more in Bioplastics manufacturers emerging unlikely beneficiaries of abundant U.S. shale gas
US demand for post consumer recycled plastics is on the rise. Gains will be driven by several factors, including a growing emphasis on sustainability among packaging and consumer product manufacturers, advancements in processing and sorting technologies allowing a wider variety of plastic to be recycled, along with continued support by federal, state and local governments for recycling efforts will also provide a significant boost to recycled plastic collection, processing and demand. Read more in US demand for post-consumer recycled plastics to rise to 3.5 bln lbs in 2016
Weakness in Europe’s rotomoulding sector can largely be attributed to the continued economic uncertainty in the continent that resulted in the reduction of infrastructure projects and impacted on the demand for rotationally moulded water and fuel tanks, which make up the largest end use application for this process. To know about the application sectors that have been impacted negatively, those unaffected by the recession, factors driving growth for IBC, etc, Read more in Rotational moulding industry in Europe experiences cautious recovery, growing well in India
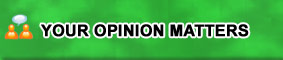
Interested to know about formulation and processing for wood plastic composite compounds and local availability. What are the additives, masterbatches used? Please advise on WPC applications, processing, raw materials, machinery required for extrusion and compounding
If I am using a laboratory 2 roll mill to process recycled and virgin PVC pellets (3-4 mm in size, hard due to fillers) with a color material to check mixing, what gap should I keep between the heated rolls in the start of the process? What should be the approx temperature in deg centigrade for both rolls?
While designing a product, I cannot get a shiny surface with Glass Filled PP. What alternatives can deliver a shiny finish without having to over-mold the product?
If i shoot a half inch per second, how many inches per second am I shooting past the gates on a 8 cavity mold.
For getting glass finish and to remove moisture, what chemicals are to be added for second grade PP granules products
If I am using a laboratory 2 roll mill to process recycled and virgin PVC pellets (3-4 mm in size, hard due to fillers) with a color material to check mixing, what gap should I keep between the heated rolls in the start of the process? What should be the approx temperature in deg centigrade for both rolls?
While designing a product, I cannot get a shiny surface with Glass Filled PP. What alternatives can deliver a shiny finish without having to over-mold the product?
If i shoot a half inch per second, how many inches per second am I shooting past the gates on a 8 cavity mold.
For getting glass finish and to remove moisture, what chemicals are to be added for second grade PP granules products


