Thin shrink film is also known as collation shrink film because it is used to pack a
number of units of packaged products together. Generally such film is made from polyethylene (PE)
because of good impact strength and flexibility requirement.
In 2006, the collation shrink market was a EUR 1.2 billion business in Europe accounting for nearly 800,000
ton consumption of polyethylene resin as per a report by Applied Market Information Ltd.
It is expected that collation shrink film will grow at least by 3-5% by surface area in Europe,
but not by weight, due to weight reduction on account of down gauging. The present market of
just about 800,000 tons will remain practically static in the coming 5 years.
In recent years there have been considerable developments in the types of polyethylene
materials used, which in turn has led to changes in film structure and thickness. Among
all PE grades, LDPE has been found to be more suitable for this application because of
its ease of shrink characteristics. It also provides good clarity that is required for
showing the contents of the packaged stuff. Over the years, the material used for this
application has changed. Currently, Metallocene grade of LLDPE is being used increasingly.
Similarly, bi modal LLDPE grades are also used to help in improving the mechanical strength.
Cost factor is the primary driver for developing the use of these two types of PE. Down
gauging is a factor that is increasingly determining the selection of type of PE material used.
The development of metallocene and bimodal LDPE resins has considerably changed the structure
of collation shrink films in recent years. Metallocene resins were hardly used in 2000, but
their use has been growing at rates of over 60% pa in this application. Volumes are still
modest (metallocenes accounted for less than 3% of the market in 2006) but are expected to
continue growing at rates of nearly 20% pa to 2011.
In order to enhance print quality, there has been considerable development of coextruded shrink
films in order to use metallocene resins in the outer layers: this has the triple benefit of
providing a high gloss printable surface, producing a film with improved transparency combined
with the potential to downgauge the film by selection of appropriate resins for the core layer.
This last, non-cosmetic, benefit will become increasingly important as environmental initiatives
gain momentum over the coming years with the aim of minimising raw material usage.
Food & beverage markets are the prime market sectors for the use of collation shrink film.
Both these sectors accounted for more than 70% of the total market in Europe in 2006.
Healthcare sector adds about 15%. Only 15% of the present application goes for other end
uses. Food and beverage sectors are expected to grow faster and therefore will consume almost 80% by 2011.
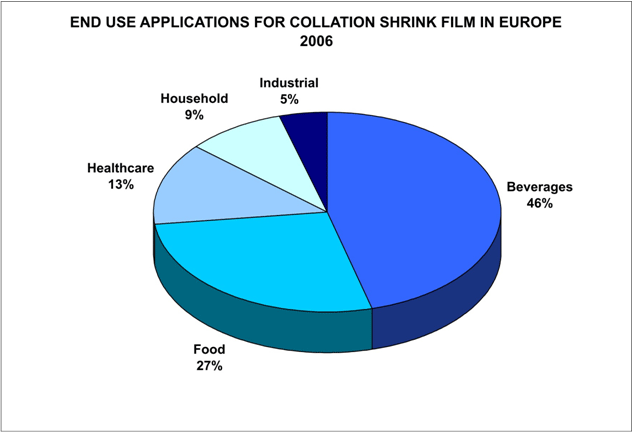
Another major shift is taking place is in terms of printed collation film. Earlier
films were meant for their functional usage but recently aesthetics requirements also
have to be met where printing is one of the most important criteria. The development of the collation shrink market will primarily be driven by the growing share of
food and beverage purchases through supermarkets in southern and central Europe combined with
further concentration of sales through supermarkets in northern Europe. Supermarket shopping supports
the sale of products in multi-packs, particularly in the beverage sector and this in turn is leading
to growing demand for printed collation shrink films. Major producers with in-house printing
facilities will have considerable advantage as the demand for printed films is forecast by AMI
to grow from 12% of the market in 2006 to 19% in 2011 � nearly doubling in tonnage terms.
{{comment.DateTimeStampDisplay}}
{{comment.Comments}}