OSS-SMC is a method for producing light weight parts, by employing
a sandwich structure of SMC in HOT press moulding. This SMC sandwich
component is nothing but SMC(Sheet Moulding Compound) with two layers,
the outer layer is SMC (based material) and the core layer is "foamed
SMC" (SMC+blowing agent).
The main advantage of this process is reduction in no. of steps
in production process (Hence the name "One step process").
Thus it is a cost savings method. Many of the vehicle parts that
the currently being made of conventional SMC, could soon be replaced
by OSS-SMC components.
The sandwich structure of SMC improves the rigidity of the product
compared to conventional SMC component. The comparison is by subjecting
the materials to area load. The different materials show clearly
the light weight construction potential of OSS-SMC. OSS-SMC is 34%
lighter than a conventional SMC and 56% lighter than steel.
Material Selection
The Material for outer layer is a standard low shrink SMC, which
was modified in such a way so as to fulfill the process requirements.
The core layer is based on a conventional SMC with a low glass flibre
content and at 30 to 40% by volume, contains high volume of SMC
recyclate. The sandwich component thus constitutes a mono system
which can be recycled without need for material segregation. An
alcohol is used as the blowing agent.
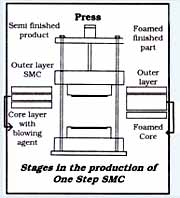 Production
 Production
Process
The figure shows the process sequence of the One step sandwich
SMC.
For producing SMC sandwich component, the process sequence
includes three phases pre pressing, foaming and curing.
First, the SMC foamed core is formed by adding blowing agent
to the SMC. Then this multiplayer SMC blank is laid flat in
the compression mould in a HOT press moulding machine and
pre pressing is done. Once the mould has been filled, the
foaming process , necessary to give the desire sandwich thickness
takes place. The foaming pressure of the core material ensures
that the outer layer remains in contact with the mould surface.
After outer layer is cured, the mould is opened with simultaneous
foaming of core layer. Then the part is demoulded.The structure
of this moulded part corresponds to that of 'constructed sandwich
SMC' whose outer layers are made of conventional SMC. SMC
sandwich made by this process does not need to be completely
flat, but can be geometrically structured, for example with
spherical curvatures.
|
Conclusion
Earlier, the production of a sandwich component with classical
outer structure and core layer is not acceptable because of higher
production cost, due to more steps involved during production. But
this ,one step method reduces the number of steps involved, also
this method is suitable for producing 3D curved parts and the parts
can be recycled without the need to segregate the materials.
OSS-SMC can be preferred for vehicle utility parts such as roof,
door, floor and rear wall. Add on parts such as hinges, gas pressure
springs, lock catches and radiator grills can be attached directly
to the OSS-SMC. No support structure is needed.
Further development of this process is aimed at increasing the
performance of sandwich system in terms of its mechanics and surface
quality.
Previous Article
Next Article
Tell Us What You Want
Windmoller and Holscher 5 layer cast film line
| | | |