Barrier packaging
protects products from infiltration or in some
cases, exfiltration (the passing out from the
container) of contaminants, of flavor, color,
odor, etc., as well as preserving the contents.
Barrier resins are polymers that are used in packaging
to provide a barrier to some unwanted intrusion
in or out of the package. Barrier resins block
passage of several important substances, including
oxygen, moisture, odors, flavors and others. Plastic
barrier packaging has shown significant growth
since the discovery and development of the first
synthetic specialty barrier resin, polyvinylidene
chloride in the 1950s and 1960s. The commercialization
of ethylene vinyl alcohol (EVOH) came a bit later,
in the 1970s. The barrier properties that are
very critical are: Oxygen, Carbon Dioxide and
Moisture. Unfortunately, sunlight and store lighting
cause color fading, vitamin loss, and generally
compromise the most carefully designed product
and can damage branding image and credibility
by low taste or poor visual appearance. For obvious
economic reasons, the food, detergent and cosmetics
industries constantly search for solutions to
extend the shelf life of their products.
As per a new market research
report from Business Communications, the demand
of barrier resin in USA in 2004 was about 2.7
KT and is expected to grow at 8% to reach about
3.9 KT by 2009. There are 3 basic applications
markets of barrier resin. The largest is food
and beverage packaging, which accounts for more
than 90% of the U.S. market. Other smaller but
important markets include chemical/industrial
products packaging (including automotive gasoline
tanks) and healthcare products packaging such
as blister packaging. There are essentially 3
different types of products in the category of
barrier resin:
- Barrier resin
- Permeable film
- Tie layer resin
- Ethylene-vinyl alcohol (EVOH) copolymers,
the highest oxygen barrier resins are now commercially
produced and most used in the U.S. for food
packaging.
- PCTFE, the fluoropolymer polychlorotrifluoroethylene,
the highest moisture or water vapor barrier
resin is mostly used for pharmaceutical blister
packaging (PBP) for drugs, which are very moisture
sensitive.
- Nitrile resins, copolymers of acrylonitrile
(AN) with methyl acrylate (MA) are used in food,
chemical/industrial and healthcare packaging
- Polyamide (nylon) barrier resins, primarily
oriented nylon 6, is mostly used in food packaging,
and is also used in chemical/industrial and
healthcare product packaging.
- Thermoplastic polyesters, primarily PET is
by far the largest market since we include the
use of PET as a carbon dioxide barrier resin
in beverage bottles. This market is expected
to continue to constitute more than 90% of the
barrier resin market as it grows at an AAGR
of 8.3% through the forecast period.
Tie layer resins are adhesive
resins used to bond together dissimilar resins
in the increasingly popular multilayer barrier
packaging structures (MLS). Typical tie resins
are copolymers of ethylene with vinyl acetate
(EVA copolymers) or an acrylic comonomer. These
tie layer resins are expected to grow at 5.5%
from 75 KT in 2004 to almost 100 KT in 2009.
Trends in the barrier plastic packaging market
include the continuing development of more complicated
and sophisticated multilayer barrier structures,
using more but often thinner layers. Perhaps
the most exciting ongoing development is the
multifaceted effort to increase the barrier
properties of PET to make it a suitable material
for packaging beer. Several new methods have
been developed and now are being tested. This
market could present a significant new opportunity
for PET in barrier packaging.
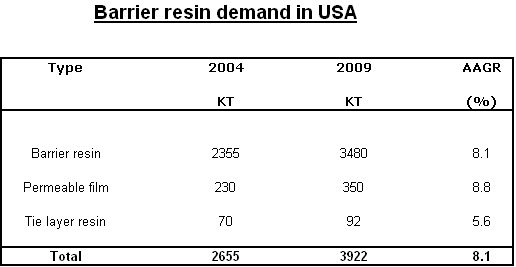
Current barrier packaging plastics are good,
but problems that restrict their use or hinder
their growth remain in many applications. These
include:
- High Cost:
Cost of barrier resins
is almost always higher than the cost of a
simple monolayer plastic package of LDPE or
LLDPE.
-
Susceptibility to contamination
or degradation especially by moisture:
EVOH is the best example of this problem,
since its hydroxyl groups give it good barrier
qualities but also make it susceptible to
hydrolysis. As a result, EVOH only can be
used as an inner layer in a MLS.
-
Recylcing or Disposal problems:
Since most barrier packaging contains more
than one type of plastic, recycled is difficult.
-
Challenges from competing
materials:
Silicon oxide glass coatings can provide a
superior barrier.
|
{{comment.DateTimeStampDisplay}}
{{comment.Comments}}